Launching Design Domain
Materiality.
What does the term materiality mean to us, in our processes, experimentation, our making and critical thinking?
How do our ideas materialise?
What does material awareness mean in our discipline?
You are to explore and consider interpretations of the word within the many contexts it is used, such as material or structural qualities.
My research and physical experiments with different materials has led me to exploring how textile materials can co-exist with technology. This proposal shows my research into material waste produced by fast fashion and lays out my plan for Part 2 for how I will utilise material waste through upcycling, recycling and technology driven zero waste strategies to create a new artefact.
Research
Textile consumption
What of waste can be used?
Tangible tech
Things like smart glasses, headphones and headsets.

Environmentally friendly
Material breakdown
How can the material return to earth?
Is the material regenerative or degradable or like resin or plastics be harmful?
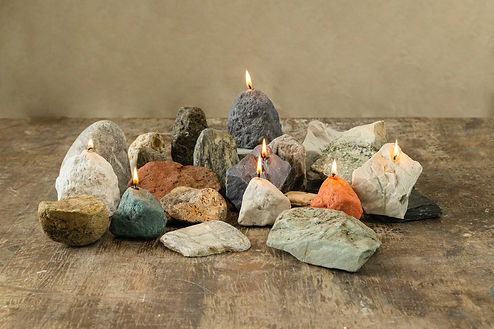
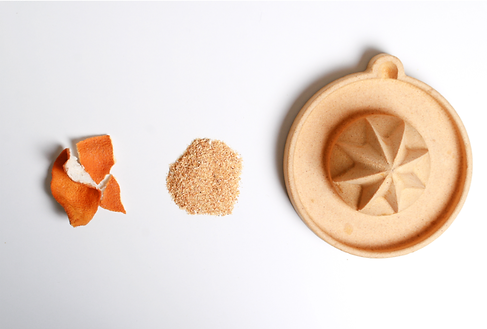

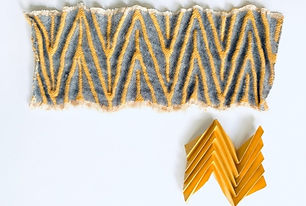
My first kind of research started with the panel discussion. Artist Christina Wong stressed about production transparency between business and consumer, for example where a brand chooses to produce, what they pay they their workers or how they source raw materials. I liked this idea because we are aware that not every process can be completely sustainable but the honesty around these processes makes a difference.
I found Alkesh Palmers and Ella Burleys use of the natural and abundant materials within their environments an interesting concept. Burley’s use of the commonly found sugarcane broken back down into a raw material and used to cast bowls, showed me how social and cultural significance can play a role in an artists choice of material. Burley wrote “over time sugar has become under-appreciated and devalued. Through an appreciation of craft and traditional production techniques Ella has transformed Sugarcane from a humble crop into a crafted artefacts.” Burley as well spoke about an object’s life. What happens to an object after it is disposed of? How can the material break down? Is the object truly ‘recyclable’? These questions have led me to be far more aware of waste and the bio-degradable component of a material. Palmer's use of orange peel tapped into this kind of thinking by using waste to create a product linked to the original wasted item in this case orange peel rind. I enjoyed Stefanie Cheog's use of natural and found elements interesting and cost effective.
Technology Meets Fashion

Iris Van Harpen
I started to look at some well known designers who are using technology as a way to help reduce waste within their designs and create visually stunning pieces that by hand would be impossible. Laser cutting is prominent in Iris Van Harpen’s practice. This dress example utilised laser cutting and 3D printing to ensure material accuracy, manipulate the material and create a finish that would be impossible without technologies aid. I like Harpen’s use of technology to mimic natural elements like water, it creates a juxtaposition between process and material.

Kate Goldsworthy
Kate has perfected a laser cutting textile practice that allows her to cut a fabric in specific lines that then lets her construct a final garment. Goldsworthy is one of the leading textile designers when it comes
to environmental awareness. She has a project ‘ASAP Paper Cloth’ which involves her creating her own fabric out of wood and plastic fibres to create completely zero waste garments. In this example she had made this sheer material out of 100% recycled materials.


Julia Koerner
Julia Koerner is my favourite examples of how technology influences material construction. Her collection ARID included a jacket that was entirely 3D printed, by entirely I mean even down to the joins in the fabric and all structural components. Her design starts purely in digital form which means there is no physical material waste up until the point of final construction. The effect of the final fabric is mesmerising as it looks like a soft malleable texture but is in fact plastic. I love the spikeyness of the jacket and how it looks like it could move.

“The perpetuating cycle of over production and consumption relies on the use of natural resources that contributes substantially to environmental degradation,” said Kerry Bannigan, founder of the Conscious Fashion Campaign.

Useful Reads
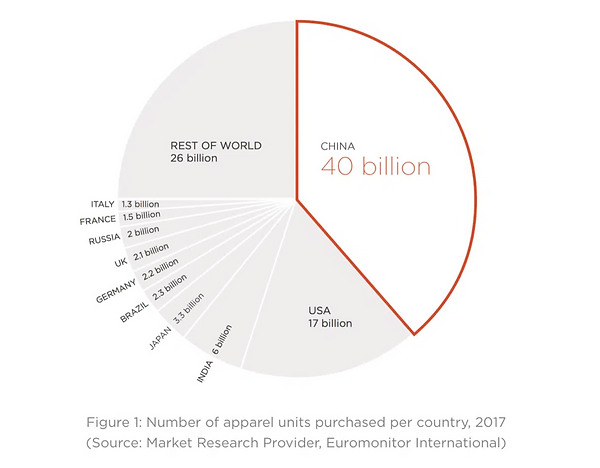

Circular by design is the practice of putting waste at the forefront of the design process. Thinking about how an object will be broken down pre production. I like this way of designing as the global stat of only 12% of materials being recycled to me was alarming. This is because though clothes are constructed not to be broken down properly meaning because of production techniques clothes can be made un recyclable. By designing for disassembly it allows us to fully utilise material.

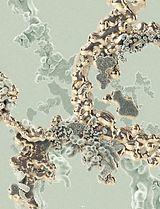
This Lithuanian studio made these 3D renders using microscopic algae as the texture material. I like natural materials and the visualisation of data through these abstract patterns. How are elements made tangible? Can data be made tangible? Think of the unwearable and how to materialise this.
According to Selfridges, more than 60 per cent of its customers want to shop sustainably and 90 per cent want to buy less, but better - while the social and environmental impact of a purchase was found to be important for 84 per cent.
Process
This was me starting to find a workflow for creating a prototype. I'm starting to consider what materials and softwares I will need for part 2.


Branded clothing vs fast fashion
What differs? Is it just social factors or how are the garments actually constructed? Are they consumer conscious? Are they environmentally sustainable? Does the product involve waste? How long will the product last? What are key physical differences? Looking at luxury shops like Selfridges more luxury brands are definitely attempting to be more transparent about processes and material consumption as well as improved material quality.


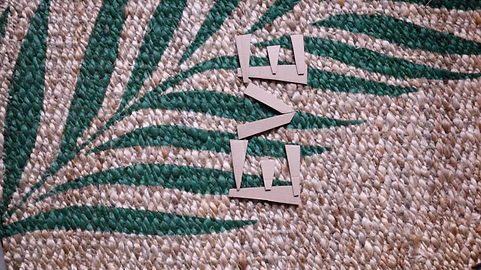

Process Film
I made this film as a process vlog of how I made the immaterial signature into a tangible prototype.
What materials will you use to make mock ups if you are trying to be conscious of waste and environmental impact?
I thought about this a lot since I'm being so careful in my material choice for the rest of the project. I like using waste materials like cardboard, scarp paper etc so that's exactly what I did. Using my dogs food boxes I carved EVE's signature out to create a faux leather kind of poster design to show what the branding could look like on 'fabric'.
How will I take the shapes of her signature and visualise this for technology?
Well I had thought about the lasercut and for that I needed to make vector shapes on Illustrator. For printing I need to make extruded shapes on a 3D modelling software probably Blender.


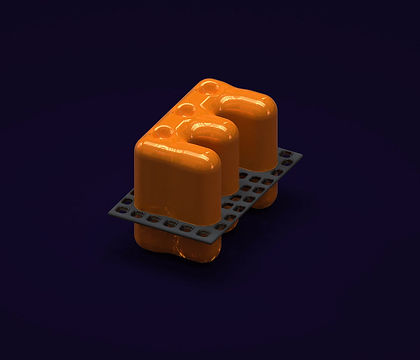
Making digital prototypes to avoid material waste. What finish do I want? What colours am I thinking? How will the fabric sit in the print? Look at depth and texture either negative space or extruded texture. I made these mockups in WOMP and I feel they turned out pretty well.


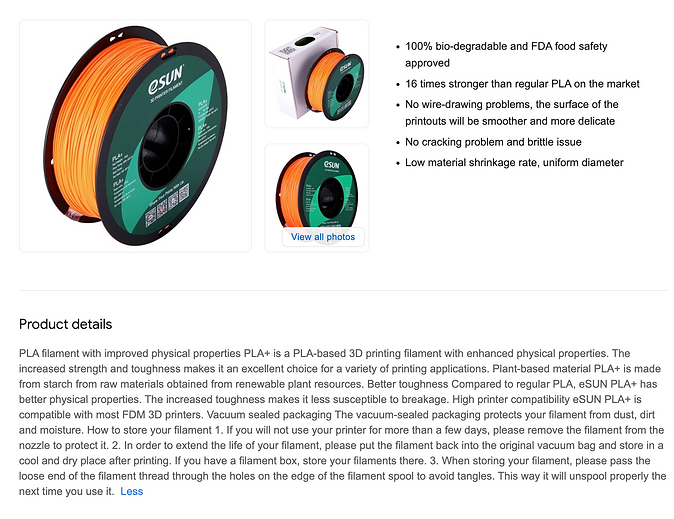
Daviy is a 3D printing textile designer who works purely with biodegradable materials. I liked her pieces and her material consideration.
Eve was dead set on the colour orange to go with her theme for the bag.
I bought two orange filaments one PLA and one PHA.
3D printing is great in terms of being able to turn anything really into a 3D model however the process requires a fair bit of energy and some filaments that the printers use can be toxic and harmful. Some filaments are coated which emit fumes, some filaments are non degrading and others are made from plastics. PLA is normally made from corn starch which is a good option but I wanted to see what other environmentally safe options there was. I looked at recycled filaments made from filament waste, which people had reviewed saying it was prone to warping and some of these filaments although recycled were non degrading. I looked at ways to use my filament waste to create new filament DIY style although this proved tricky and would require sending it away and spending more money. I found natural filaments called PHA made out 100% natural based products, PHA is made from the digestion of microbes whereas PLA is made from raw materials from plants. This was the best option for me as it allowed me to consider how this component would break down and I could source from the UK at a very reasonable price. I also found PLA made from sugarcane which is a great option for biodegradability. PHA is both compostable and biodegradable in marine environments whereas PLA is compostable but may stay for up to a thousand years in the marine environment. PHAs biocompatibility is another important aspect
This is the piece of writing that initially introduced me to circular design.
It is making me consider how are materials broken down back to a raw material?
How garments are constructed for deconstruction?
How can we consider the waste process pre disposal?
Sketching & Sourcing
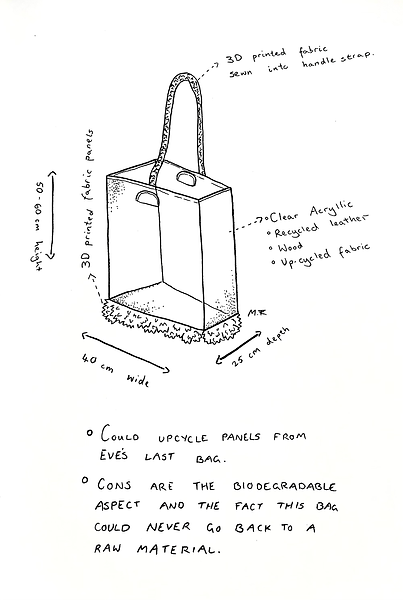
Sketching different bag designs. What is the functionality of these designs? How do people interact with the materials? Are the moveable, looking into modular fashion. What elements can we upcycle?
Can we use objects that are already constructed or part constructed? What about throwaway culture, retro design and vintage reclaim? What if the fabric was a sheet?

How can the materials be experimented with, specifically industrial materials like wood, metal and stone?
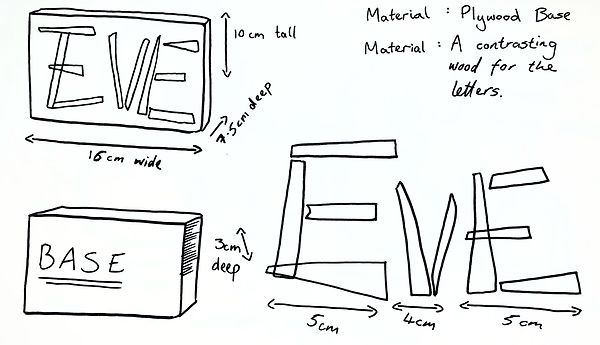


My final sketch of the branded bag design. I'm considering how large I want each component. Is scale of the branding to play a larger role in the context of the bag? Can each letter be different? What size of bag am I thinking?
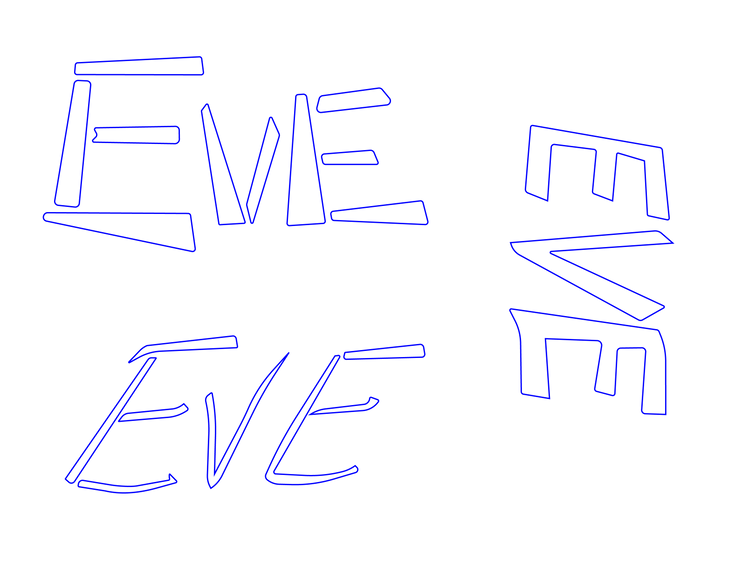
For a prototype I used the vector shapes I had created tracing EVE's signature and made this into a laser cut file. I had opted for a wooden prototype specifically plywood since it is strong, durable, moisture resistant and the production of it is significantly less waste and energy than other woods. Plus plywood has a nice finish to it. Unfortunately due to strikes I couldn't get the cut for the presentation however this is the file and what they would have looked like. I instead hand carved the letters out of foam and attached these to my prototype poster pictured next to my process video above.

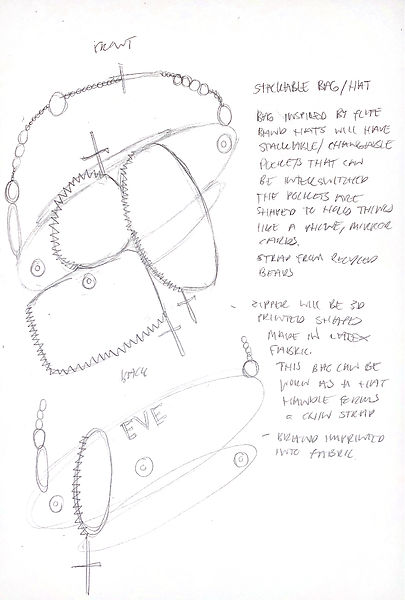

These are the 3D renders of what I imagine the model to look like with the mesh fabric through it. I made the material a plastic as to resemble the 3D printer.

Final Export
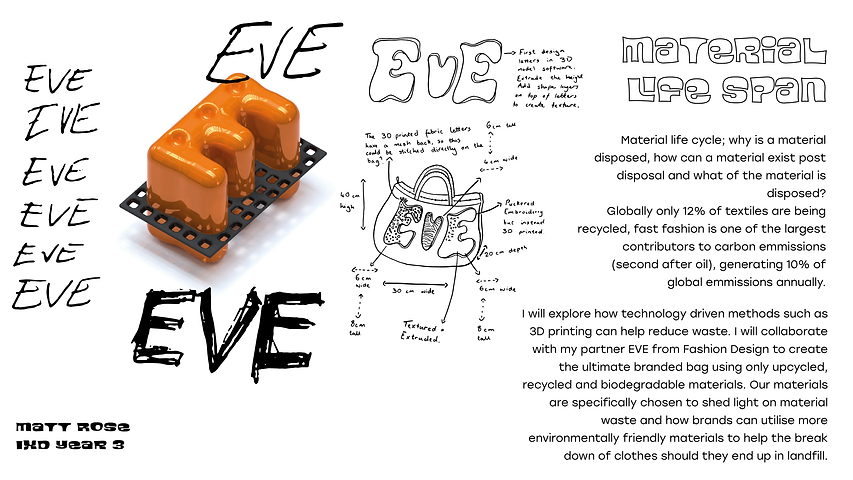
Part 2
From Part 1 I continued with my original proposal which was to collaborate with a Year 4 Fashion Design student to create a branded 3D printed fabric that will degrade. The fabric is to be used to accessorise a completely upcycled bag.
We are making this bag with our key theme of 'MATERIALITY' in mind. Our research has led us to explore material waste, circular fashion vs fast fashion and how materials in the fashion and textile industry can be returned to a raw form.
Sustainability was a term that was prominent in our research in Part 1 however in the fashion industry the term 'sustainable' is unregulated. This means that there is no enforceable industry standard for what a 'sustainable' piece of clothing actually is. Since there is no criteria for this, brands could use as little as one recycled fibre and still be allowed to brand the item as 'sustainable' even although 99% of the materials or methods are not sustainable. Upon learning this we wanted to instead be completely transparent about our use of materials and how we treated the materials. If we want to say we are sustainable or environmentally conscious we want to be able to back that up through our process.
Going Forward
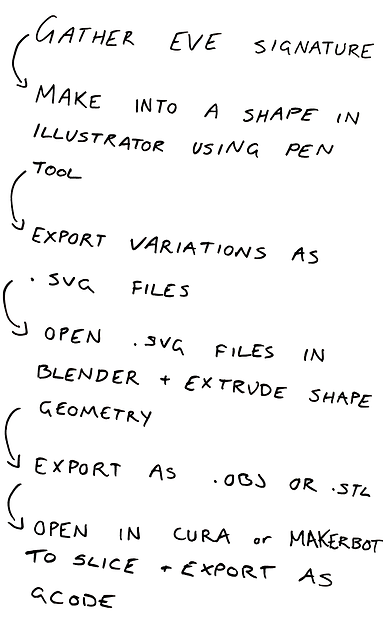
I made a to do list for the project for everything I thought I would need to do.
EVE's signature and handwriting is a really important aspect of this. The branded fabric we created to be a statement playing into the fast fashion discourse. Our research showed huge material waste produced by fast fashion brands such as Pretty Little Thing, Victoria Secret and BooHoo. We also found that brands like these are not always more environmentally conscious despite having policies in place that are meant to ensure green deals made with the fashion industry.
Victoria Secret for example signed the Greenpeace “Detox my Fashion” campaign aiming to eliminate all hazardous chemicals from its products and supply chains by 2020. At this point, it is still unknown whether the brand met that target. It does not seem to have done anything to reduce its environmental footprint, and the products are mostly made from unsustainable and synthetic materials. Take BooHoo as well, the Environmental Audit Committee published a report naming Boohoo as one of the least sustainable fashion brands in the UK. These brands are churning out poor quality unsustainable clothing at a rate like no other. We wanted our branded fabric to represent something different.
Design for disassembly and degradation.
We want EVE the brand to not be another contributor to waste in the fashion industry but instead be able to return to the earth or have our materials be reused/recycled.
By putting her name on this we are trying to say we are proud and transparent about our use of materials, our processes and our message.
Sketching


These were my initial sketches after Part 1. I knew what materials I was planning on using and generally how the process would work but to help me visualise what these models could look like I drew out quite a few variations. EVE has a keen focus on inclusivity and I thought it would be a cool idea to bring some accessibility into the sensory aspect of my models. We started researching braille and how someone who is blind or partially sighted could also interact with the garment. We were using her name as the design so it was fairly easy to translate these letters to braille and model from there.
Artist Talks
I attended the artist panels on zoom and I really enjoyed the panel discussion with artists Christopher McEvoy, Melody Uyanga Ramsay and Max Warren. These artists although were in the textiles and jewellery industry were still very interesting to listen to in terms of experimentation with materials and the ethics of sourcing materials. I liked when Chris was talking about how working with clients can sometimes make you as a designer question ethics when the brief isn't exactly how you yourself would like to utilise materials like the project he just did with fur and feathers. Melody really focussed on environmental ethics which was really good for me to hear considering that's what myself and EVE are really engaging with in this project with our choice of materials. Melody answered a question that was basically saying do you let your ethics guide you to your choice of materials and she gave a really great in answer which in summary was "yes!" We as designers know the impact our choice of material can have so she was saying before you even start to physically experiment let your ethics guide your process and artistic choices. Max gave a pretty good answer about this as well saying that he only makes so many pieces a year because he doesn't want to needlessly waste materials or over produce since to get the raw materials (metals) he uses can be quite harmful to the environment. A good point raised by all them was that not every material we use can be 100% ethical or sustainable all of the time but to recycle, reuse and look at new ways of gaining these materials is really important to try and minimise impact as much as we can and always be completely transparent about how, why and where we got the materials from.
Process
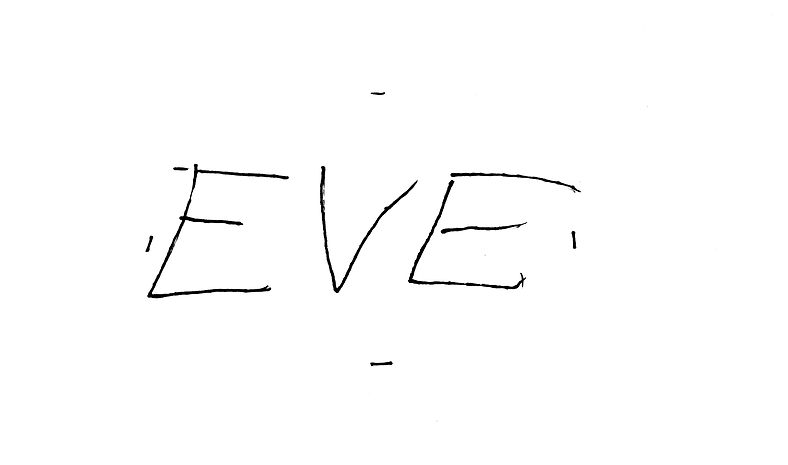
I had sketched a fair bit of what I'd like the models to look like and this version of EVE's signature was perfect for sizing. I went into the Fashion studio and measured the smallest and largest areas that I could cover. This was a pretty accurate size for what Eve wanted, (about palm width).

I then went into Illustrator much like I had done on Part 1 and traced vector shapes using the pen tool over her sketched out writing on a layer above. This was great for us since the shapes were coming out as close to her writing as possible which I think was a nice effect.
The important part in this stage was exporting. In blender if you import a svg file not only can you extrude the geometry but the pen points are still editable should I want to mess about with the shape post extrusion.

This was me now working in Blender to extrude the shapes. After I was happy with sizing, depth and shape I could export as either a .obj or .stl to then be sliced for the printer. I've been trying to use Blender a bit more and I'm getting more comfortable with the interface but for this task the workflow was super simple and once I got in the swing of it I was able to make quite a few variations of models.


I watched the 3D printing workshop on Planet Estream to remind myself of what I needed to do. These were the sizes for the print bed which was good to bear in mind, although once you opened the model in the slicer they were very easy to rescale. I had to download the MakerBot software and then you just import those .obj files, choose the Replicator 2 from the device menu and export as a .x3g file.




Found scrap mesh fabric. This one I didn't end up using. I thought it would've been better since it was more discreet and more of a solid fill however it was too thin and flimsy.
Locally sourced net fabric. This one I did use and it was perfect! the colour matched the models, the stretch was ideal and you could tug it and there was no ripping. The print nozzle also didn't damage this one at all.
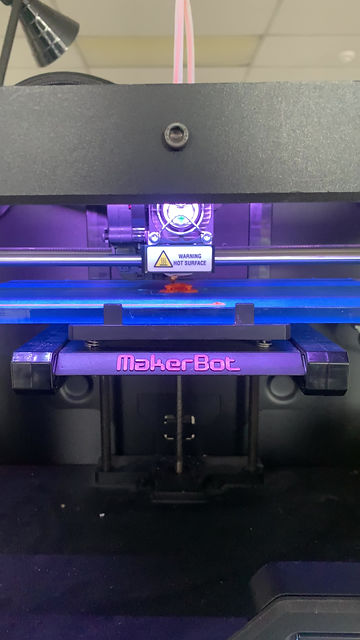
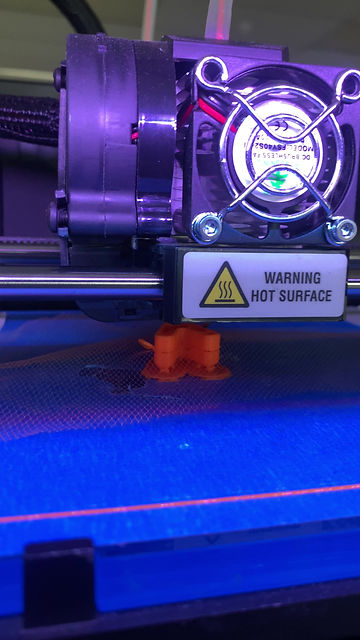
This was my very first time using the printer and my first experiment with the fabric. I was super happy that my idea worked and I had a few points that I noticed could be improved. I was being a bit too eager when pausing the print then putting down the fabric meaning that the fabric wasn't far enough intertwined within the model. I knew I wanted the model to be secure so I had to do put the fabric far enough in but not too far that the model then wouldn't sit flush when sewn in. I settled on stopping the print anywhere between 40-55% finished to put the fabric down. I also noticed that I really had to secure the fabric to the print bed otherwise it was getting burnt by the print nozzle. The fabric I used this time I also noticed was a bit too thin and flimsy despite it being a more solid fill net. Going forward I changed fabrics to a less solid but more durable net. Unfortunately after only getting to do 3 models disaster struck and the next day the printer broke. I'm not going to lie this was a bit stressful since other departments and TSD weren't exactly forthcoming in letting me use their 3D printers since I was going to be using the fabric and apparently that was 'too risky'. I was also dead set on using my own filament since EVE wanted specific colours and I had sourced my PLA and PHA filaments in Part 1, TSD said this would be impossible as they only use their specific white filament. I finally managed to get access to a 3D printer when I went to the Interior Design Studio and spoke to the head of department Tony. I can't thank him enough and I was extremely grateful he was so relaxed about me using it.


Interior Design <3

I had never used this printer before and to be honest I had only kind of figured out how to use our one in the studio after being shown once. I thought it couldn't be much different and I looked at some manuals before setting up. I had to use a different slicing software called Cura and this model of printer was different as well, this was an Ultimaker 2+. The file type this printer recognises is .gcode so I had to change my files that I had export to .x3g. I managed to get access to this printer for two days and I was there from 11am to 5pm both days.
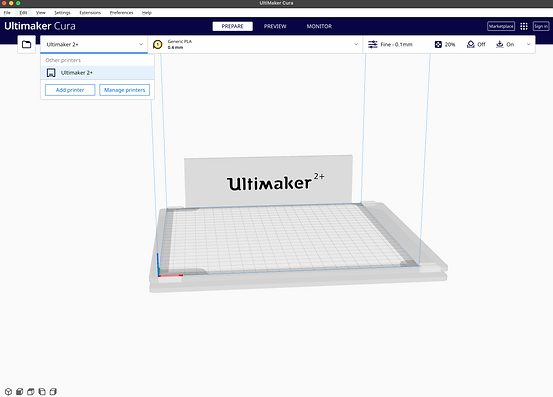
How It Works



These were my favourite images from the printing process. It shows how the model starts, how the model looks during the cold pause when the fabric is places on top and finally how it looks when the print is finished and the model has printed through the fabric.
This was a quick process video I made just documenting my printing stages.
Final Export
updated padlet with supporting images
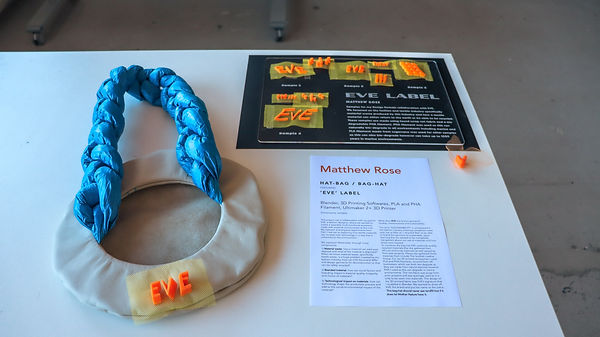




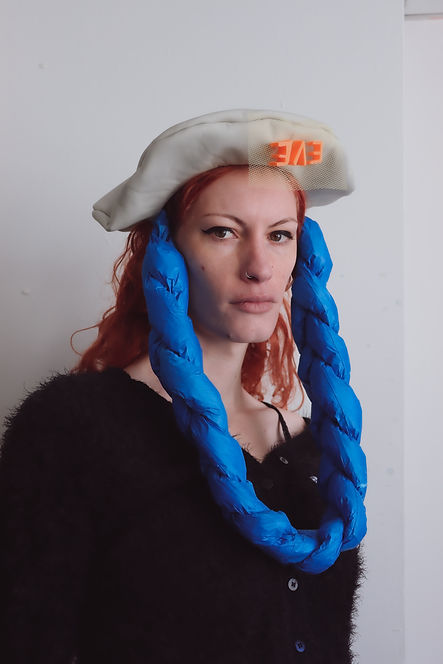
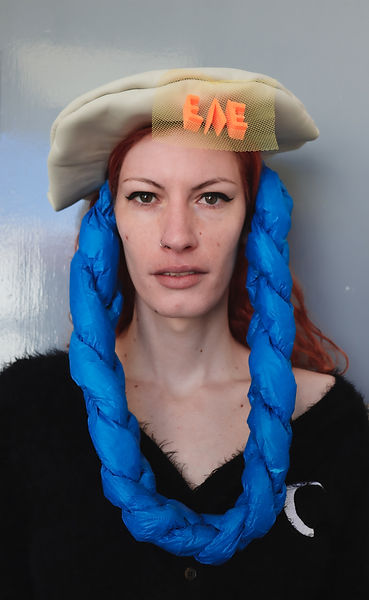


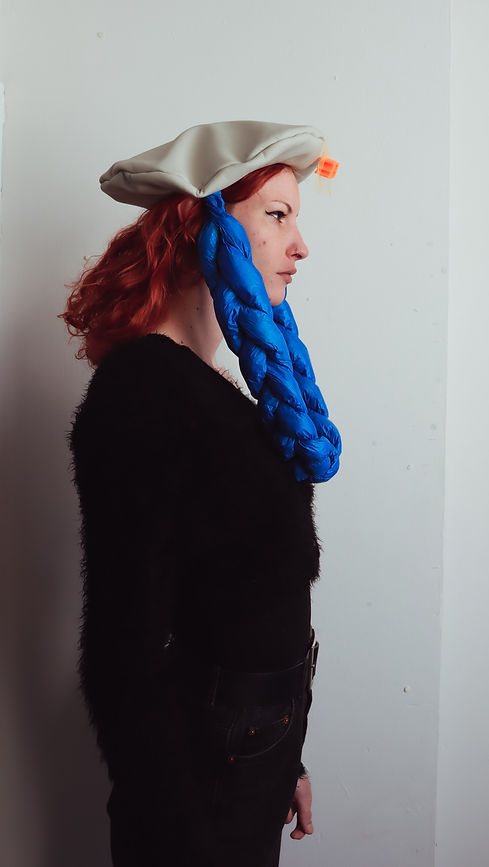
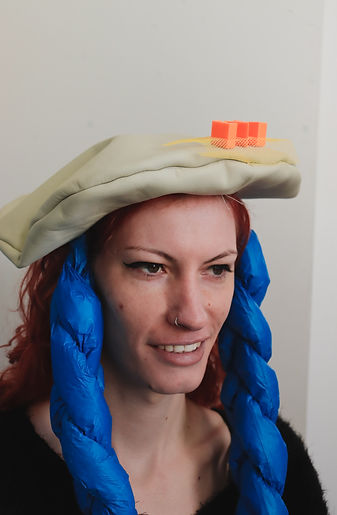


I'm so happy how this turned out despite having some issues with equipment and holidays along the way. I enjoyed the exhibition and I plan to keep 3D printing especially with textiles an on going project. I will keep my journal updated with more samples and final images of the hat bag.
